Options
Restringing problems
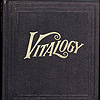
Hey all. I can restring my electric fine except for the high e string.
I have snapped 2. I need a good method for how to start it. Like through the hole in the peg then below/above etc the string. Someone fill me in on the secret. A quick step by step would be a life saver.
I was also wondering if I can have a 13 as my high e string. I have 10-52s but I have an extra 13 around and no 10. Would there be bad effects of having a 13? I mean I would only be increasing the gauge of 1 string. Or does it not work that way?
Help me out guys
I have snapped 2. I need a good method for how to start it. Like through the hole in the peg then below/above etc the string. Someone fill me in on the secret. A quick step by step would be a life saver.
I was also wondering if I can have a 13 as my high e string. I have 10-52s but I have an extra 13 around and no 10. Would there be bad effects of having a 13? I mean I would only be increasing the gauge of 1 string. Or does it not work that way?
Help me out guys
I miss you already, I miss you always
I miss you already, I miss you all day
I miss you already, I miss you all day
Post edited by Unknown User on
0
Comments
♪ Juli ♪
As for how to string a guitar, can you tell me what type of tuner's you are using? Are they locking, vintage?
A safe way to go. Take your time. Make sure you aren't binding anywhere and begin to tighten slowly.
Take up the slack a little bit at a time.
ONce you get an idea as to tension and slack, you'll be running through this in no time.
Hanging at www.TheGuitarHub.com
The only Forum for players by players.......
Playing Les Pauls, Teles, Hubers, Gustavssons, Kolls through a Mad Professor amp with a Bob Burt Cab.
BJF powers my Pedal Board
My biggest problem is starting the winding. How do I get the string to stay put after its through the hole?
I miss you already, I miss you all day
1. PUT STRING THROUGH HOLE
2. WRAP END AROUND THE TUNING PEG AND GO UNDER THE STRING COMING FROM THE BRIDGE.
3. PULL THE STRING OUTWARD (COMING OUT OF THE HEADSTOCK LIKE THE TUNING PEG) CREASING IT AT A 90 DEGREE ANGLE.
4. WIND THE TUNING PEG (WHILE HOLDING THE PART YOU BEND UPWARD WITH THE OTHER HAND) SUCH THAT THE STING OVERLAPS THE PART THAT YOU CREASED UPWARD AND IT WILL THUS LOCK IT INTO PLACE.
IF YOU GET GOOD AT THIS, YOU SHOULD ONLY HAVE 1-1/2 WINGS OF STRING ON THERE AT MAX FOR ULTIMATE TUNING STABILITY.
For me, on the high E, if I can't get it to stay I wind it through the hole, wrap around half of the tuning peg and through the hole one more time. Sometimes I do it on the B as well. Just an old holdover from changing them on the acoustic.
The fender website has photos posted for proper stringing.
If they are vintage tuners, just a hole.
Bend the string so it 90 degrees, and wrap once. Then start tightening down, that is all that you should need to do.
Hanging at www.TheGuitarHub.com
The only Forum for players by players.......
Playing Les Pauls, Teles, Hubers, Gustavssons, Kolls through a Mad Professor amp with a Bob Burt Cab.
BJF powers my Pedal Board
Yep, vintage tuners are a little more difficult. But you mentioned that you had standard american fender tuners... you should not have to worry about that.
Question 2: How can I tell if this gauge is too heavy and I need a setup?
I miss you already, I miss you all day
I do not understand question 1, but to answer your second question..... You need to intonate your guitar any time you change sting guages. If you notice that the neck is bowing, notes are buzzing in certain areas, etc.
You can do all of this yourself, it is very easy.
Take into a Fender authorized tech for a set up. It will be less then 50 bucks and he might even let you watch
It isn't difficult to adjust saddles on a strat, but I would never tell anyone to fuck with the truss rod, NEVER!
Hanging at www.TheGuitarHub.com
The only Forum for players by players.......
Playing Les Pauls, Teles, Hubers, Gustavssons, Kolls through a Mad Professor amp with a Bob Burt Cab.
BJF powers my Pedal Board
as long as you have an understaning of how the instument works, you know how a truss rod woks, move it in VERY small incerments at a time (in the right direction) you will have no problem.
All this can be learned with a basic physics understanding of how materials react to applied forces. Or a decent book by Dan Earlwine on setting up a guitar.
okay, maybe it is not for everyone... i am an engineer and that stuff comes second nature to me mybe i take that for granted sometimes.
Do as JofZ says, take it to a qualified fender tech. it does not cost that much.
I've been here for a couple of years now, and someone else finally knows of Dan! :cool:
I've pasted this link so many times and it should be federal law that anyone with a guitar should have this
http://www.stewmac.com/shop/Books,_plans/Building_and_repair:_Guitar,_electric/Guitar_Player_Repair_Guide.html
You can have a 13 for the high string. It'll essentially be like having 2 b strings. It'll be fun bending it! The thing you might run into is that it may be too big for the nut slot, depending how deep it's cut.
If you put a 13 on there, it may either bind in the slot, or possibly end up widening the slot so that if you ever go back to a 10 gauge it'll rattle in the larger slot.
I'd stick with the 10. It'll be a louder e string and might overpower the b string.
For a strat, I always like the locking method. I'll go find a diagram somewhere and be back.
If you have enough slack to have three wraps on the post below the hole, you put some downward tension on the nut for a nice tone, too.
Don't be mankind. ~Captain Beefheart
__________________________________
Yeah man, i came accross Dan about 4 or 5 years ago on the LPF, i have traded a few emails back and forth a few times on ideas and such. He is a master craftsman and an expert luthier to say the least. His instructional packages are worth its money in gold. I also like that he is very old school and does most or all his work with his hands (or his trained workers).
Dan is the cream of the crop!
Yup,,, and a great player, too! We went out to Ohio once to visit his shop when we were making guitars, and he took the time to show us all kinds of secrets. (the secrets flowed a little better when the beer flowed!
Not only that, but Jorma Kaukonen was hanging out there, too.
I can't find a diagram of my favorite way to string a strat, but I'll find one yet!
Here's a link to the Mr gear head strat set up guide anyway:
http://www.fender.com/support/setup/stratsetup.php
I think it's relatively easy to adjust a truss rod, but you DO have to be careful. Like Moe said, subtle adjustments and don't do it if it seems scary. It's a good thing to learn, though if you play a lot. A Strat or Tele are the best to learn on, too. Just a bunch of screws and nuts and bolts holding those together! :cool:
The worst things that can happen are if you are trying to turn a truss rod nut on an old guitar and it is rusted, and it breaks. So don't force anything or work on old guitars if you don't know what you're doing.
And don't turn too far, like more than 1/8 turn to start.
Well, you won't need to do that anyway if you're sticking with the same gauge strings.
Don't be mankind. ~Captain Beefheart
__________________________________
That is awesome you have been to his shop, i have seen many photos of it, that is it. My favorite photos were of his reincarnation of the Albert King V guitar that he made for a customer this past year. UNBELIEVABLE!!!!
The dude I was making guitars with and I had a running joke after we were there. We were measuring and suddenly we were in the league of 11/64ths!
Dan was showing us how he drilled for bridge studs, or something like that, and he said, "I use an 11/64ths drill".
We were laughing like,, "whoa,,, we're just guitar players! We never KNEW there was such a thing as 11/64ths!"
He's such a great guy. My friend had an original Flying V (One of 80!) It had a broken headstock, and Dan wouldn't touch it. He referred us to Mike Stevens in Houston. So we road tripped it down there from Ohio and he repaired it. Stevens is an unbelievable scientist at that stuff, too.
I actually learned a lot from Eric Schulte, if you ever heard of him. He lived right near me and I spent a lot of time with him (about a hundred years ago, it seems).
Don't be mankind. ~Captain Beefheart
__________________________________