Options
Renovating/Finishing a Basement
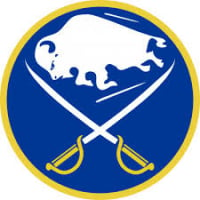
Currently, I am prepping to finish my basement. Kind of a mish-mash of R&R and Sabres...
I am looking online at many people who seem to put up foam board insulation up against the concrete wall. The particular renovation I read takes 2" and then a layer of 1/2" staggered.... which leads to a great rating.
I already have some sort of pre-installed insulation on the top 3/4 with a vapor barrier. Would it be stupid to remove this and go with foam board? Or should I keep it and just put up the framing around the "baggie". I cant find any examples of anyone working with this type of thing, nor can I find anyone who suggests removing it or keeping it.
I also plan to seal the walls with Drylok Extreme and some cracks with some Polyurethane concrete/masonry sealant. Thinking of coating the floor with something too. Going to also do some work on the outside to slope away, longer drain spouts, etc...
I also have those tie-rod/form things sticking out of the wall. What is the best tool/method to removing these? Stupid builder.

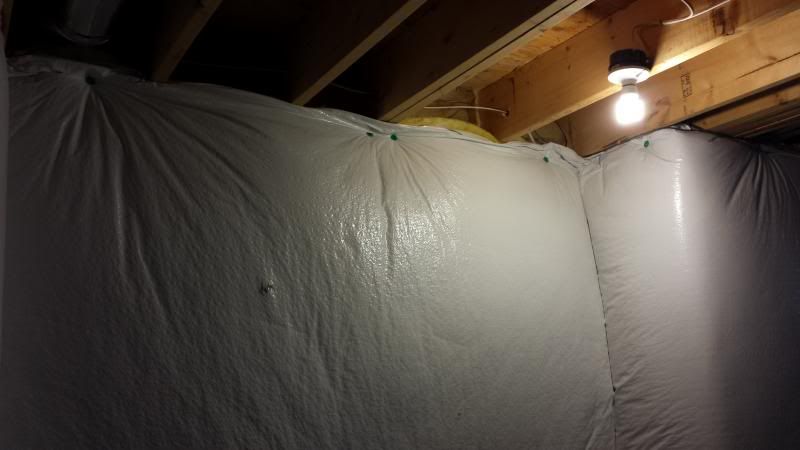
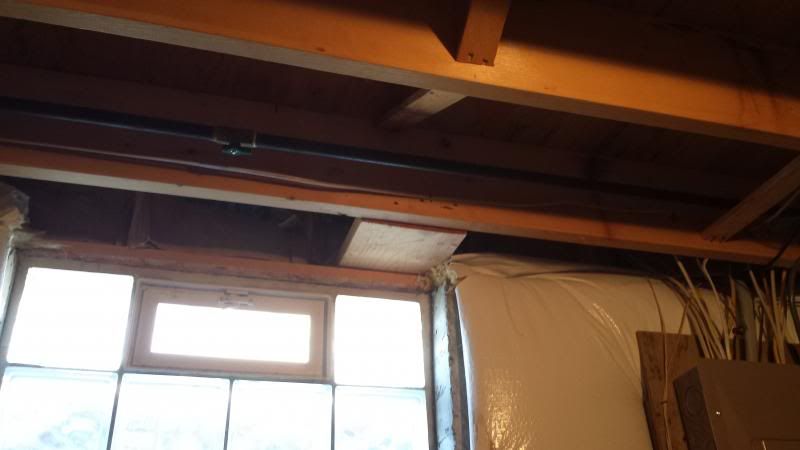
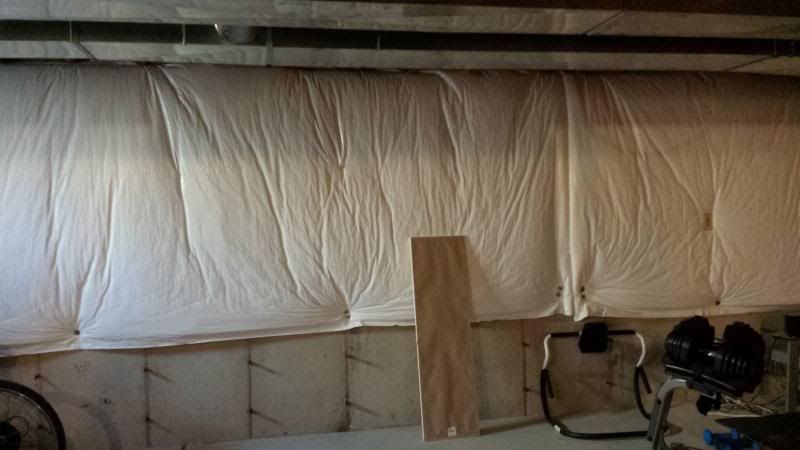
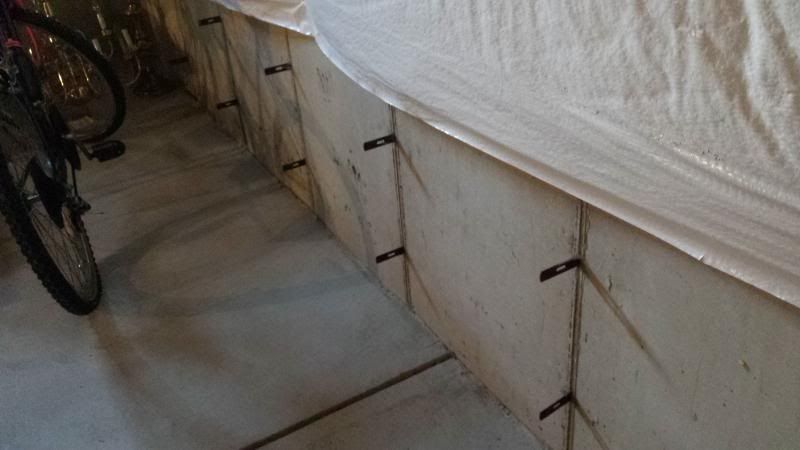
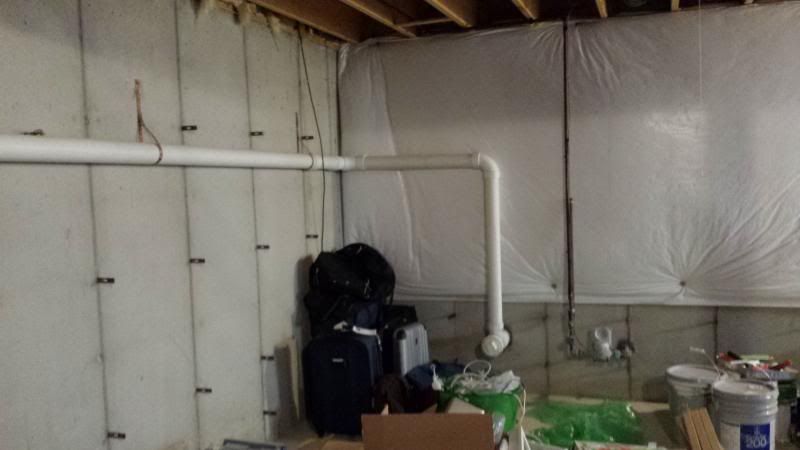
This is the mechanicals and what will be the unfinished storage area. Going to grab more shelving for the area pretty soon
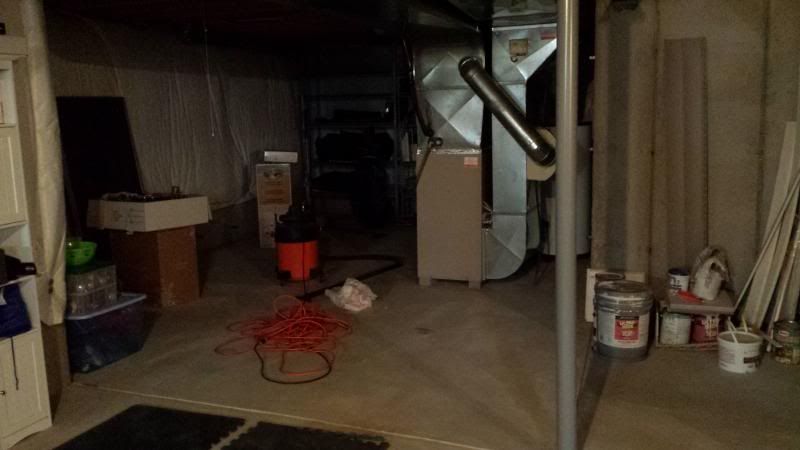
and here is the basic floorplan. Gotta update some shit I changed.

I am looking online at many people who seem to put up foam board insulation up against the concrete wall. The particular renovation I read takes 2" and then a layer of 1/2" staggered.... which leads to a great rating.
I already have some sort of pre-installed insulation on the top 3/4 with a vapor barrier. Would it be stupid to remove this and go with foam board? Or should I keep it and just put up the framing around the "baggie". I cant find any examples of anyone working with this type of thing, nor can I find anyone who suggests removing it or keeping it.
I also plan to seal the walls with Drylok Extreme and some cracks with some Polyurethane concrete/masonry sealant. Thinking of coating the floor with something too. Going to also do some work on the outside to slope away, longer drain spouts, etc...
I also have those tie-rod/form things sticking out of the wall. What is the best tool/method to removing these? Stupid builder.

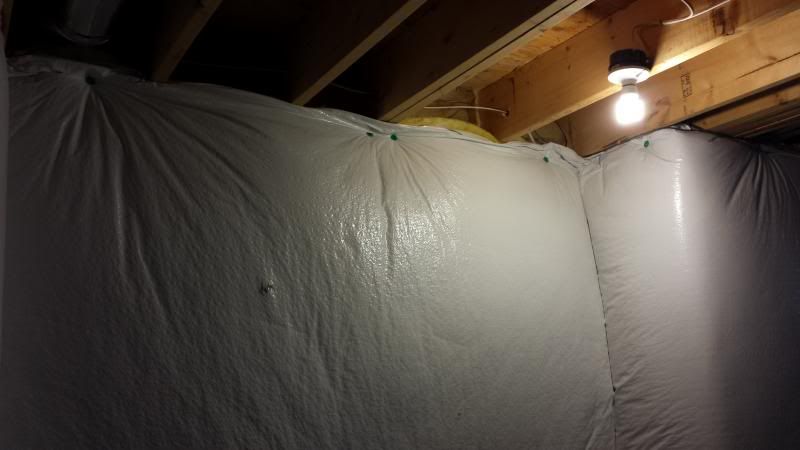
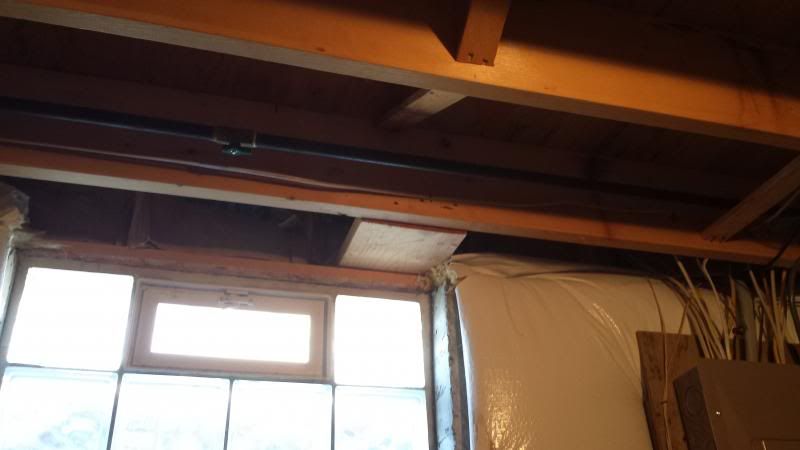
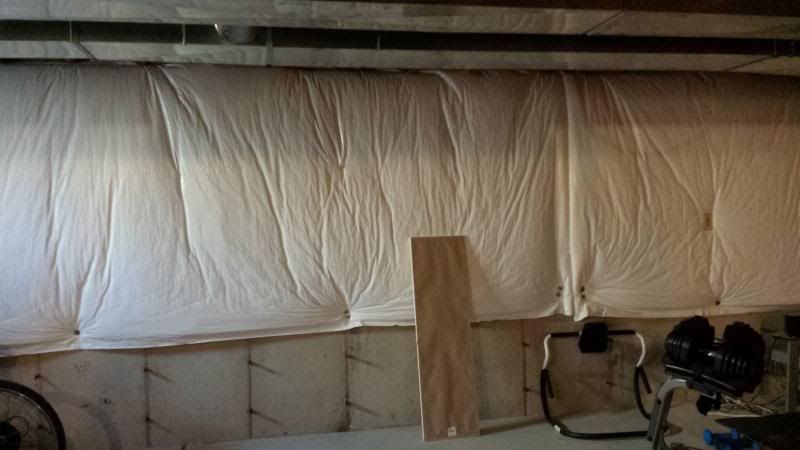
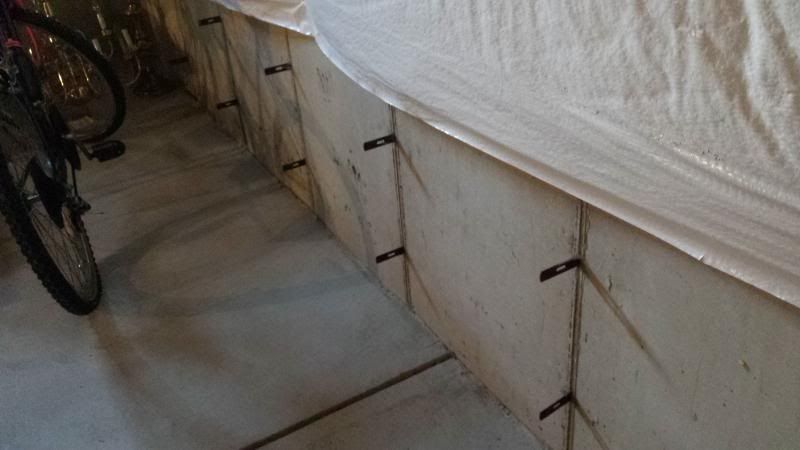
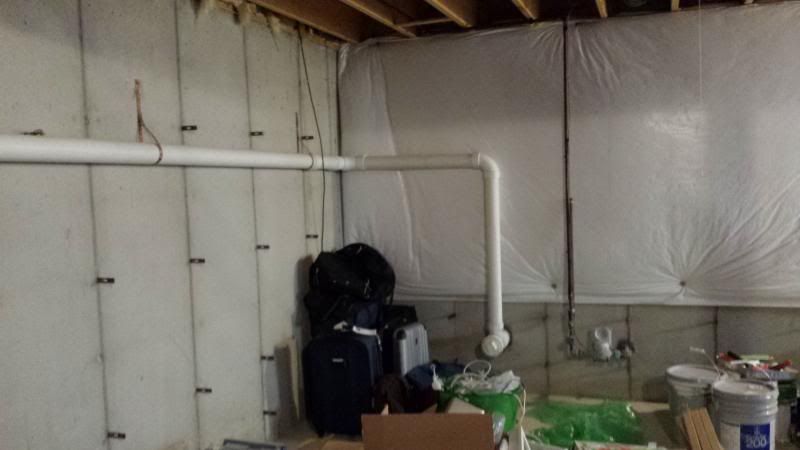
This is the mechanicals and what will be the unfinished storage area. Going to grab more shelving for the area pretty soon
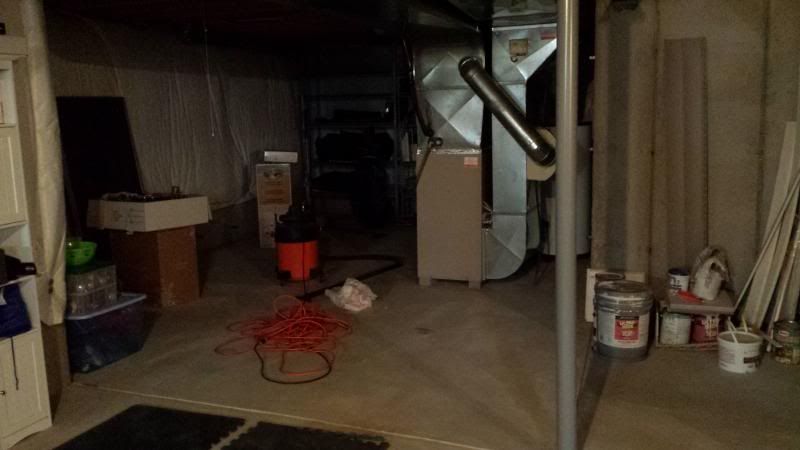
and here is the basic floorplan. Gotta update some shit I changed.

Post edited by MayDay10 on
0
Comments
I would go with foam board insulation personally. Remove the bag insulation. By applying foam board you can ensure all areas are covered and there is no cracks in insulation barrier. If you aren't that worried about letting heat scape/cold seeping in then you can just build around what you have and put some fiberglass insulation on the bottom 18'-24' that is currently exposed.
The things sticking out of the concrete are "concrete form ties" that held the exterior and interior concrete form walls together while they poured the concrete. They can be removed by clipping them with diagonal cutters, twisting and or rocking them back and forth as close to the base with vise grips or pliers. Some concrete will come off so do this first.
Local hardware stores often are a wealth of knowledge.
Also build yourself your own shelves out of 2x4s and plywood for decking, cheaper and more rugged.
Wind this thing up.
The basement is dry. However there was a lot of dead pill/potato bugs around the perimeter. I called the exterminator and he said it is because it was damp. So I got a nice dehumidifier. This winter we had a few feet of snow at one point, it melted along with 2 straight days of rain. It stayed dry, but I did notice a damp spot in one area where storage would be between the floor/wall. Just damp looking, no standing water.
So right now, based on research I am leaning toward removing the bag. Apparently the fibrous insulation against the concrete wall in my climate invites mold. Then I would remove all the steel form ties with a hand mallet. Then patch those areas with a compound or caulk gun, do the same with the cracks (no moisture cracks), and seal with Drylok. Also inspect the entire perimeter and caulk/patch/seal any breaches and clear caulk around pipes that go through.
Then 1" foam wall bonded/glued with the concrete, sealed appropriately, and also cover up to the floor up above. Probably going to do this on all interior and exterior concrete walls.
Then the framing goes up against that, with batting insulation between studs, complete with moisture resistant drywall and at least 2 coats of latex paint.
And I dont trust contractors. I called 2 for pricing. They were all over the place, not much detail in their quotes, wasnt really sold that they wouldnt cheap out or cut corners... plus I would rather take my time, spread the budget out, save some money, learn, and take more pride in it. I do have a friend who is an electrician though who I am going to call on.
I am building it to code with one exception. I am not having an egress door/window. That would tack on an additional $5K or so, require punching through my slab, digging a huge hole somewhere in my yard to provide this eyesore (which seems to be a hazard on the topside). I am not getting it permitted/inspected. I dont want the headache and my already ridiculous taxes increased.
Wind this thing up.